3D Printing and Additive Manufacturing, time to consider it in your business? Product Design Melbourne
As far back as the 1950s we have been dreaming of one day having machines capable of replicating or producing any object our heart desires. Since the 1980s engineers around the world have been busy designing machines that may one day turn this dream into a reality.
With big companies such as Boeing and Adidas beginning to take 3D printing technology seriously and find ways to utilise it in their own businesses, we decided to take the opportunity to sit down with Tim Naylor, Business Development Manager of 333D in Port Melbourne and get a feel for how 3D printing technology maybe able to benefit your business.
Q: As someone who has undertaken a Masters in Additive Manufacturing, what excites you about 3D printing technology?
The exciting thing about additive manufacturing is that it captures the imagination and extends the boundary of what is possible.
3D printing is democratising production, enabling the design and manufacturing of custom products to be accessible to the masses.
Previously you had to worry about tooling, minimum order quantities, geometrical constraints on mass produced parts, now you just need a computer and access to a 3D printer and the average Joe can produce their own creations.
Q: What improvements are you looking for in printing technology? What will that allow the technology to achieve?
The key improvements we are looking for in 3D printing technology is the speed of printing, range of materials and cost of production.
3D printing has historically been a slow manufacturing process, with some prints for large objects taking a few days using FDM (Fused Deposition Modelling) technology, which could take 30 seconds using injection moulding.
Newer resin printers are dramatically decreasing 3D print time. Companies such as Carbon 3D are claiming that their technology will (in future) rival injection moulding, enabling mass customisation of manufactured parts.
Resin printing or light based solidification of liquid offers the fastest printing technology category and with the widest range of resins.
The companies who are pioneering resin printing are hiring mainly material scientists who are extending the range of materials that can be 3D printed.
There has truly been remarkable progress in the past few years in increasing the range of materials, and this widens the scope for 3D printing.
The other component is obviously cost of production. 3D printing needs to become cheaper to enable mass customisation production to replace traditional mass production.
Q: With current technology, what are some of the most exciting products that you have seen produced using 3D printing at 333D?
An entire bathtub using an SLS (Selective Laser Sintering) printer, a 3D printed weather chart, a giant translucent syringe one meter high, and our figurines of real life scanned people, have been some of the most exciting.
Q: Are there any areas of business that you can see potential for 3D printing, where you believe that the technology is currently being underutilised?
The architecture and building industry are dramatically under-utilising the technology. For producing architectural models, the technology is now faster, cheaper and more accurate, than a person spending weeks with balsa wood and a laser cutter, manually assembling a scaled architecture model. 3D printing has the potential to seriously disrupt this market as you can print 100’s of highly accurate architectural models in the one print run, within a few days. There is also the capability to print some of these models in colour. This allows architects, property developers and even home owners, to physically view a scaled model of a design, at a fraction of the cost and lead time of a handmade model.
Q: Metal printing is a fairly new 3D printing method and comes in several forms. Can you tell us a little more about the different methods, and their strengths and weaknesses?
There are two predominant metal 3D printing method, Selective Laser Melting (SLM) and Electron Beam Melting (EBM). They essentially involve the use of directing a laser or stream of electrons onto a bed full of metallic powder. The laser or electron beam, traces out the cross-sectional profile of the object and the object is built up layer-by-layer, by fusing the metallic particles together.
The great strength of 3D metal printing is that you create very complex intricate lattices structures, that you can make any other way.
The aerospace industry is probably the greatest user of 3D printing, as you can create components that have been hollowed out or you can reduce assemblies, optimizing a components strength to weight ratio. It’s also being applied in the medical industry for custom implants that are tailored to the patient, with latticing for promoting tissue integration, parts which can’t be machined.
The big drawback with metal 3D printing is the cost and there are new technologies coming on the market which promise to reduce the cost of metal printing.
Q: When it comes to manufacturing, 3D printing is often disregarded because if its per-part cost when compared with traditional high volume methods, yet several big companies are now taking the technology very seriously and incorporating it into their production. What sort of components do you believe are best suited to 3D printing for production? What makes 3D printing the most commercially viable solution in these cases?
The four key criteria when assessing a commercial 3D printing application are: is the product customisable, better, cheaper or faster to print?
3D printing flips the traditional economics of manufacturing on its head, as it costs the same to produce a custom part as a standard part. Normally in manufacturing, production becomes cheaper with scale and volume, so small production runs are prohibitively expensive. This is not the case with 3D printing.
Given the economics of customization are changing, companies are now seeing the potential to customize products for their customers. For example, Adidas has entered into a contract with Carbon 3D, to produce 100,000 customized 3D printed midsoles next year. Adidas will have foot scanners in their stores and will sell custom mass produced shoes, each tailored to the individual. This will allow Adidas to differentiate from the heavy competition in the footwear market.
The medical and dental industry meet the criteria for customisation really well, as every patient and medical treatment is unique.
By better, we mean, is the object too complex to be made using a traditional manufacturing process, and can you achieve a higher quality component using 3D printing. The aerospace and automobile industries are seeing great potential for the technology as they can create lightweight complex components that you can’t manufacture any other way. For the aerospace industry, the driver is saving weight, which equates to money saved on fuel.
3D printing can also be a lot cheaper for short production runs of between 1-100 units of an object. Rather than going to the trouble and expense of getting the tooling made and dealing with minimum order quantities, it can actually be cheaper to print directly and have it delivered faster.
Companies are also interested in the concept of the warehouse in the cloud. For companies who have to stockpile spare parts for when the product goes out of production, they are interested in eliminating warehousing and shipping of spare parts and just storing their CAD designs in the cloud and printing them in the country of use, when needed.
Q: You believe that every school should have a 3D printer, why do you believe this is so important?
The technology has fantastic potential in education for enabling students to imagine and come-up with their own designs and produce them. In education, it’s not so much about the printer, as the printer is just a piece of equipment, it is what it enables you to do that matters. 3D printing enables you to build, in a relatively short space of time, any design, with few constraints. This is powerful as students can imagine new objects and new designs, build them and test them. They are not limited by conventional wisdom or conventional thinking, which has the potential to lead to new possibilities and new industries.
3D printing also enables cross-disciplinary learning. For example, imagine each student in a classroom of 30 has to design a component for an engine and each component is printed, then assembled together as a class. The students in that situation are learning design, teamwork, assembly, manufacturing and motor mechanics.These tools were simply not available when I was at school.
The technology is also important for the future of the country, as I think we are facing, another 'Banana Republic' moment, as Paul Keating famously coined. Australia is overly dependent on its service sector (e.g. real estate and cafes), construction and resources to drive the economy. These sectors are highly vulnerable to downturns and may not be sustainable wealth generating industries in the long run. Creative industries will need to be developed and this will require a creative workforce with the right education, a finance system that puts money into the new industries and a government with the right vision on how Australia will develop in the 21st century. 3D printing and technology in general, will be important in facilitating a move to creative industry based wealth generation.
Q: What does the future hold for 333D?
Our ambition is to lead the 3D printing industry in Australia and be the disrupters where this technology applies.
Tim Naylor is the Business Development Manager at 333D Limited in Port Melbourne.
Would your customers benefit from customised products? Do you have a product idea that has high value but low production volumes? Get in touch with Bayly on +61 3 9413 9000 to discuss whether 3D printing might be a part of your next Melbourne product design project with us.
Interested in new technologies? Sign up for our newsletter now!
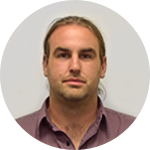 |
Ryan Mischkulnig, 17 July 2017 |
|