Case Study - Tube Stacker
Looking at new and more efficient ways of doing the most simple of tasks
Collaboration
Garden City Plastic manufactures millions of square seedling tubes annually. These were being manually stacked into stacks of 50, before being put into bags. At the production rates required, this was tying up one operator for almost half their time, adding considerably to the unit cost of the tubes, and threatening the viability of the product. The solution had to be capable of easily being moved from one machine to another as dies were moved from machine to machine. The design also had to be scalable to suit other designs of tubes that had similar properties.
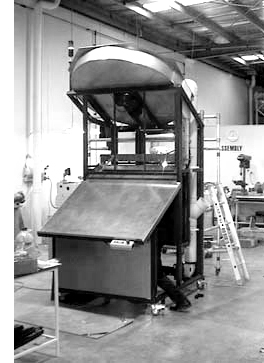
Garden City Plastics were already very happy with a tray stacker that Bayly had previously built for them. They had no hesitation in approaching Bayly to design and supply a solution to this new problem. Bayly worked with Garden City Plastics to develop a complete understanding of all requirements, including a number which were not immediately apparent.
Process
Once all requirements were clearly identified and agreed, Bayly was able to propose a concept for the machine that Garden City Plastics was very comfortable with. This concept was prototyped and tested extensively to prove it’s basic suitability as well as it’s inherent limitations, and behavioral properties. This knowledge was essential to the successful design of the final product.
Bayly designed, manufactured and supplied a machine which took the tubes directly from the injection moulding machine, and dropped them into an elevated hopper. Within this hopper the tubes were sorted and arranged so as to feed into a vertical chute, where the tubes were stacked. When the stack reached 50, it was ejected onto the storage table, from where the operators can quickly put them into plastic bags ready for dispatch.
Innovation
The final solution exceeded all requirements, including OH&S, and taking minimal floor space and operator utilization has dropped from 70% to 15%, reducing product cost significantly and ensuring the viability of the product going forward.